Gratowanie krawędzi i detali – metody, sprzęt
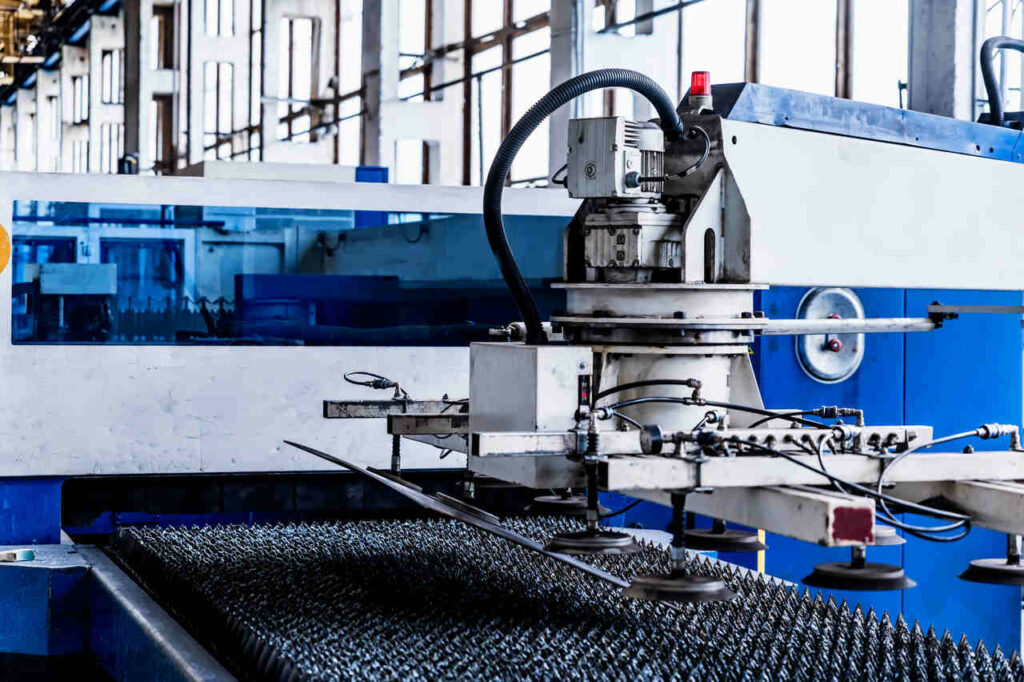
Współczesny przemysł wymaga dokładności oraz idealnego dopasowania nawet małych elementów. Z tego powodu wykończenie obrabianych części jest niezwykle ważnym elementem procesu produkcyjnego. Usuwanie zadziorów i wygładzanie krawędzi stanowi na pozór niewielki, ale wyjątkowo istotny etap pracy, który nieraz pochłania do 20% wszystkich kosztów.
Co to jest gratowanie i jakie spełnia funkcje?
Powód, dla którego gratowanie, czyli usuwanie zadziorów i gładzenie krawędzi, jest tak ważne, ma związek z wydajnością oraz bezpieczeństwem. Nierówne, poszarpane, ostre lub niedokładnie wyczyszczone elementy sprawiają trudności podczas montażu, gdy spasowanie części może być niemożliwe ze względu na złe wykonanie. Pozostałe po obróbce zadziory mogą osłabiać strukturę elementu lub oderwać się w czasie eksploatacji. W przypadku urządzeń hydraulicznych bądź silników nawet niewielki otwór lub luźny odłamek tworzywa może stwarzać ryzyko uszkodzenia bądź zniszczenia maszyny. Z tych powodów wysokiej jakości gratownice, zwane także szczotkownicami, są niezbędne wszędzie tam, gdzie trzeba precyzyjnego wykonania części, a zatem w przemyśle motoryzacyjnym, lotniczym, medycznym, a także w gałęzi jubilerskiej czy optycznej.
Narzędzia do gratowania materiałów oraz metody wygładzania
Wykorzystywane w zakładach produkcyjnych materiały wymagają specyficznego traktowania ze względu na różnice w odporności na zginanie, zgniatanie, czynniki chemiczne lub temperaturę. Z tego powodu warsztaty wykorzystują rozmaite metody wykańczania, obejmujące:
- Gratowanie ręczne – jest to najprostsza technika, a także obarczona najmniejszą powtarzalnością w porównaniu do innych sposobów. Obróbka ręczna stosowana jest w przypadku produkcji jednostkowej lub wykańczania części o złożonym kształcie. Do pracy wykorzystywane są pilniki oraz szeroka gama gratowników, jednakże efekty uzależnione są od umiejętności operatora. Nawet jeżeli mamy do dyspozycji doświadczonego pracownika, czas gratowania ręcznego pozostawia wiele do życzenia, zwłaszcza w porównaniu z poniższymi metodami.
- Gratowanie ręczno-mechaniczne – ten rodzaj obróbki wciąż polega na umiejętnościach pracownika, ale proces zostaje usprawniony poprzez wykorzystanie takich maszyn, jak szlifierki taśmowe, narzędzia szybkoobrotowe, szczotki trzpieniowe, ściernice lub frezy pilnikowe. Ze względu na udział człowieka metoda ta wciąż jest obarczona brakiem powtarzalności wymaganej podczas produkcji wielkoseryjnej.
- Gratowanie mechaniczne – wykorzystanie zautomatyzowanych procesów umożliwia osiągnięcie identycznego wygładzenia w przypadku dowolnej ilości części. Istnieje wiele technik gratowania mechanicznego, jednakże do najpopularniejszych należą metody wibrościerne i magnetościerne. Pierwsza z nich wykorzystuje ścierniwo pod postacią niewielkich kształtek, które, pod wpływem drgań, ocierają się o element i wygładzają go. Podczas obróbki wykorzystywane są gratownice kołowe oraz korytowe, w zależności od wielkości części. Drugi rodzaj gratowania wykorzystuje pole elektromagnetyczne do wprawienia w ruch twardych drobin, pełniących funkcję ścierniwa. W przeciwieństwie do maszyn wibrościernych urządzenia magnetościerne charakteryzuje się niewielkimi ubytkami w materiale, co sprawia, że jest to preferowana metoda w przypadku niewielkich części.
- Gratowanie chemiczne – kąpiel w kadzi z odpowiednio dobranymi związkami chemicznymi to skuteczny sposób, aby wygładzić nawet najmniejsze części i trudno dostępne miejsca. Płyn wypełnia każdą szczelinę elementu, a także czyści powierzchnię z niezauważalnych ubytków oraz mikropęknięć. Do tego rodzaju obróbki wykorzystywane są zazwyczaj kosze, stojaki lub bębny, które następnie zanurzane są w chemicznej kąpieli.
- Gratowanie elektrochemiczne – metoda ta wykorzystuje basen lub kadź z roztworem elektrolitycznym oraz dwie elektrody – anodę i katodę – między którymi przepuszczane jest napięcie. Proces elektrolizy umożliwia bezstykową obróbkę, podczas której ilość usuniętego materiału jest proporcjonalna do czasu oraz napięcia, użytego podczas procesu. Elektroliza nie jest szybkim procesem oraz wymaga wzięcia pod uwagę szeregu czynników (gęstość prądu, temperaturę, szczelinę międzyelektrodową, rodzaj tworzywa, rozmiar zadziorów, ciśnienie, koncentrację i prędkość przepływu elektrolitu), ale cechuje się wysoką dokładnością. Dlatego znajduje zastosowanie podczas wykańczania skomplikowanych urządzeń lub części, których nie da się wygładzić w inny sposób.
- Gratowanie termiczne – w tym wypadku element zamykany jest w wytrzymałej komorze, gdzie rozpylana jest wybuchowa mieszanka gazów – zwykle metanu oraz tlenu. Eksplozja wytwarza ogromną temperaturę, która utlenia niewielkie zadziory oraz nierówności. Jednocześnie proces jest na tyle krótki, iż nie zachodzi żadna zmiana w strukturze materiału. Ze względu na wysoką temperaturę, gratowanie termiczne nie sprawdza się w przypadku aluminium oraz magnezu.